3D Printing with PEEK, PEKK, & ULTEM™
Join AON3D's 3D printing application and materials experts for a 30-minute session that covers all the key information
Introduction
Adoption of Additive Manufacturing (AM) has sharply risen, providing a flexible manufacturing method by delivering on-demand short run parts faster and more affordably than ever before. With a large majority of businesses having validated the value of 3D printing, many are now looking to grow their AM capabilities by applying the transformative technology across their value chains. In this paper, we analyze the value of high temperature (HT) 3D printing, how it can be applied, and the cost savings it delivers compared to conventional manufacturing methods.
Material Properties
High Performance Materials, High Performance Parts
Perhaps the biggest downfall of desktop 3D printing is that printed parts often lack significant mechanical, thermal, and chemical properties needed for medium to heavy duty applications. This is due to low temperature build chambers and 300°C nozzles which limit material options, exacerbate part anisotropy, and ultimately reduce the utility of 3D printing across the value chain.
High Temperature Industrial 3D Printers, like the AON M 2+, possess the thermal conditions needed to properly print engineering grade and high-performance thermoplastics. Polymers like PEEK, PEKK, and ULTEM™ possess some of the best material properties available in 3D printing. High temperature 3D printers improve part isotropy, reduce residual stress, and ensure in-situ crystallization from the actively heated chamber, in turn, providing a significantly higher return on investment.
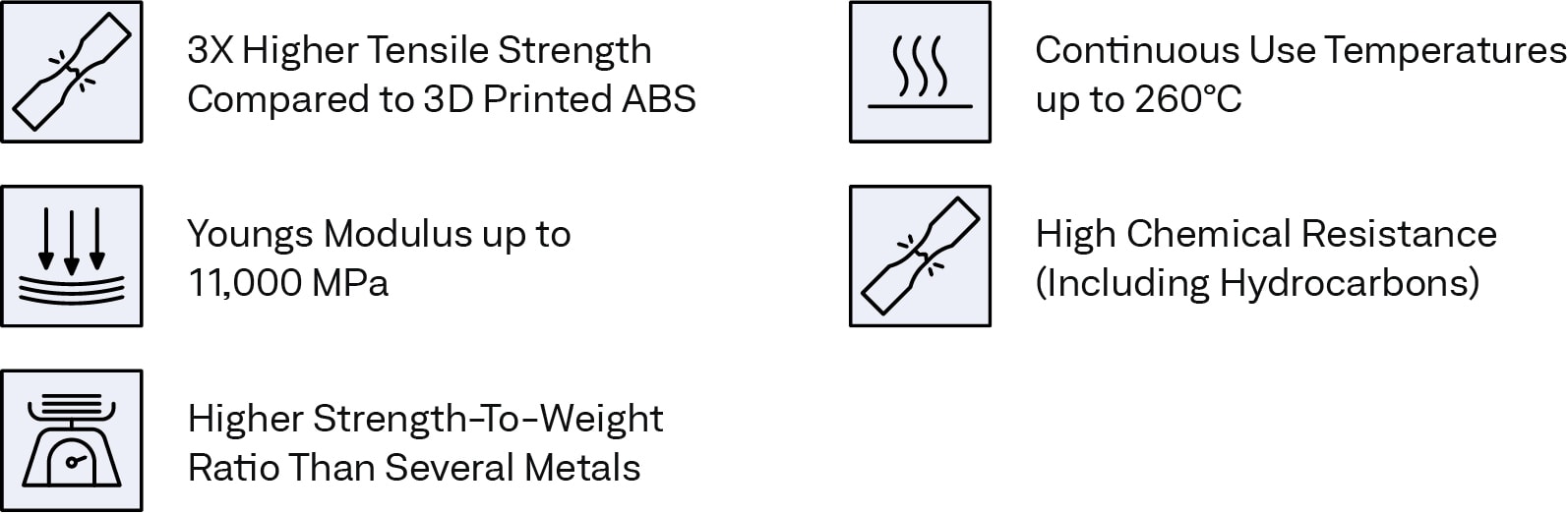
Applications
Additive Manufacturing Beyond Product Development
The ability to print parts that meet or exceed functional requirements provides more applications where businesses can reduce lead times and manufacturing costs. The list below signifies only a small fraction of ways that businesses are currently applying high temperature 3D printers. It is recommended that you connect with one of AON3D’s Additive Manufacturing Specialists to discover the full extent to which your business can benefit from HT 3D printing.
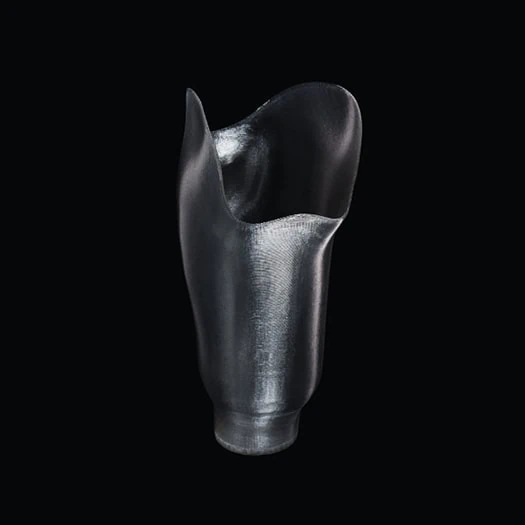
Functional Prototypes
In addition to form and fit testing, HT 3D printers can produce parts that meet functional requirements. This allows engineers to test and iterate designs in the conditions they will be subjected to.
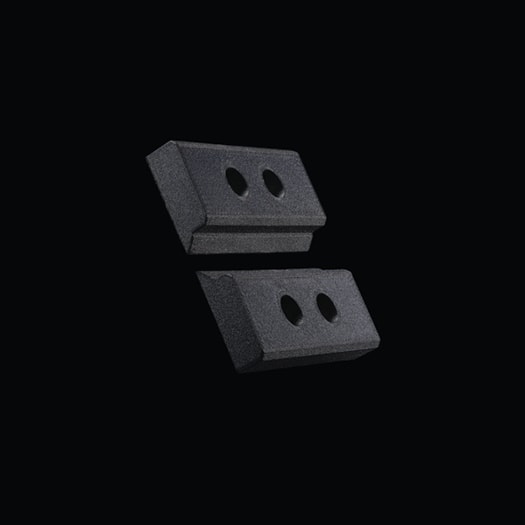
Tooling
With higher mechanical and thermal properties, engineers can 3D print high strength end of arm tooling, press-brake dies, high heat composite layup tooling, thermoform tooling, and more.
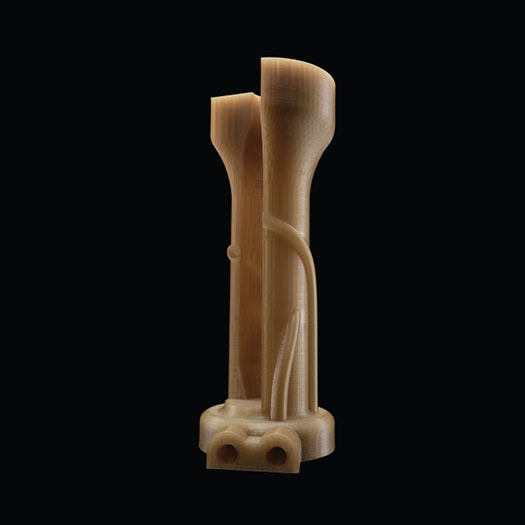
End-Use Parts
Take designs from concept to production on one machine. End-use applications include short run production, mass customization, digital warehousing, assembly consolidation, part lightweighting, and more.
Outsourcing vs In-House High Temperature 3D Printing
Transformative technologies like 3D printing have revolutionized manufacturing service bureaus, with many being able to deliver parts in 5-10 days. As seen in the following analysis, markups, lead times, and tradeoffs quickly grow with part size and number of parts needed. In this section, we compare multiple outsourced manufacturing methods with in-house, high temperature 3D printing on a per part basis.
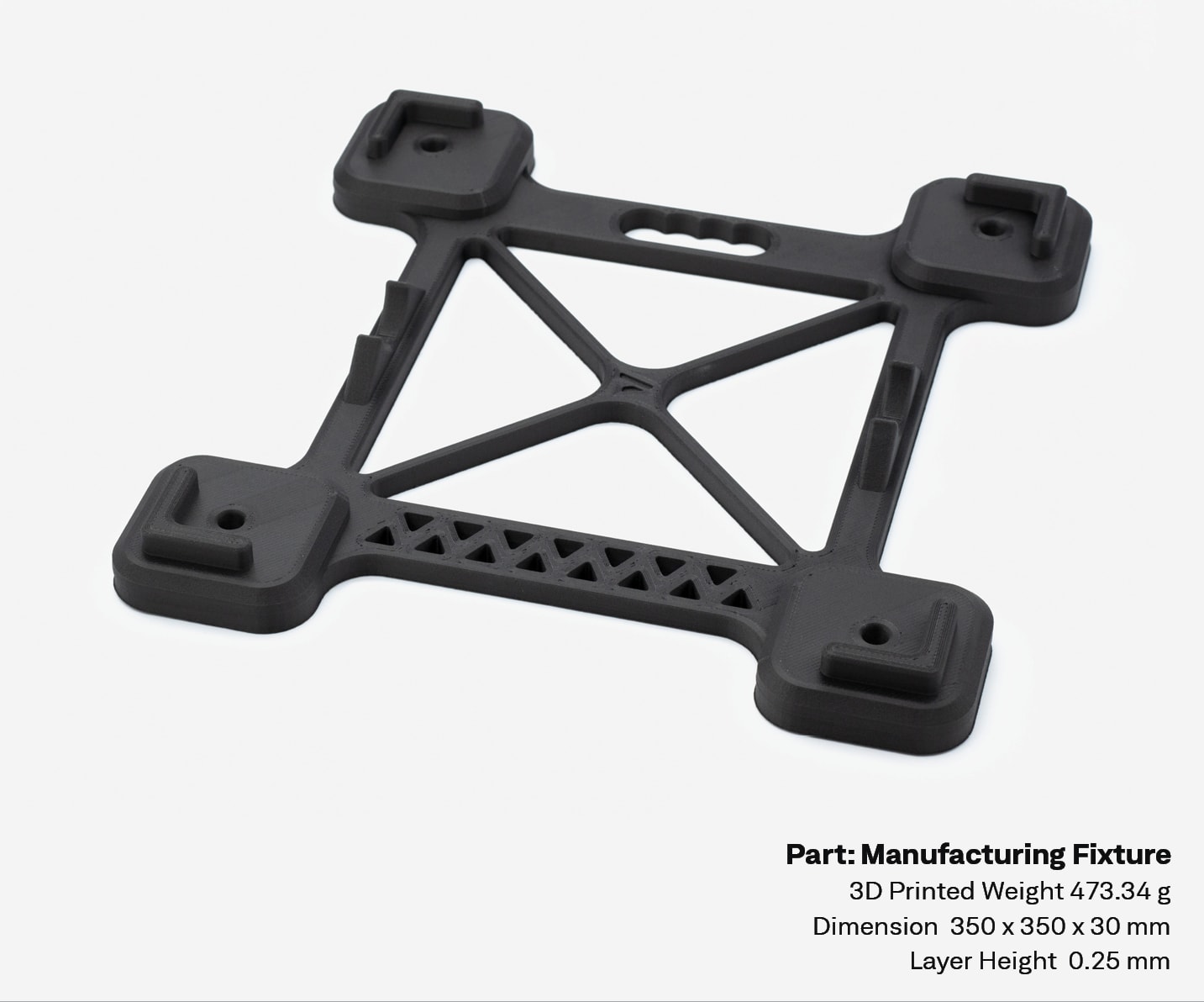
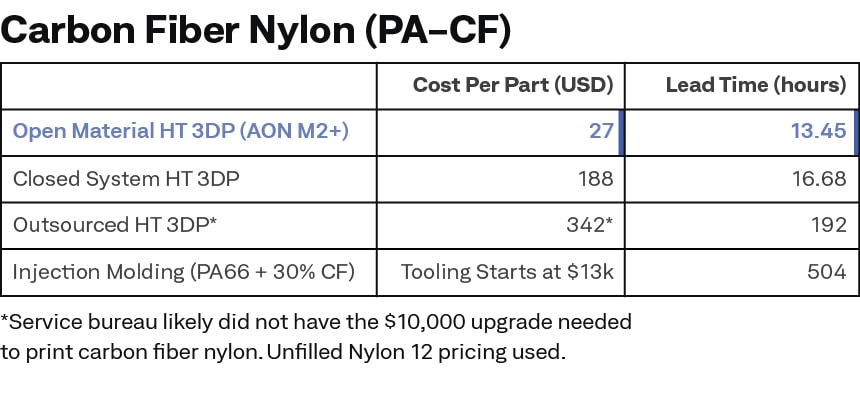
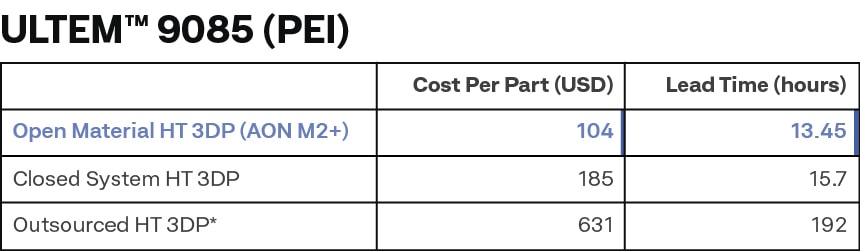
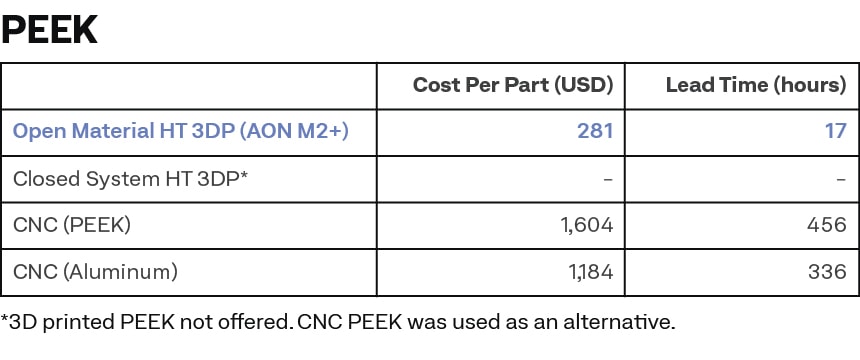
Analysis
In all situations, in-house high temperature 3D printing delivered parts an order of a magnitude faster. Naturally, expedited outsourcing options do exist but at a premium. A CNC milled peek part could be procured two business days faster for over a 100% price increase. In addition, when outsourcing, costs scaled exponentially with the part size. A 75% increase in part size resulted in a 270% increase in price.
A key consideration for investing in HT 3D printers, not included in this per part analysis, is the cost of the hardware and materials. The MSRP of the closed system was over 2.5x compared to the AON M2+, required costly upgrades and material licenses to expand material capabilities and did not offer PEEK printing. Of the 13 proprietary materials offered, engineering-grade and commodity polymers such as ABS and Nylon carried the highest markups. In their pricing structure, proprietary Carbon Fiber Nylon was more expensive than ULTEM™ 9085, an aerospace grade material, and ABS was marked nearly 690% over market price, despite no apparent improvement in mechanical or thermal properties.
Payback Period Analysis
The cost difference between an in-house 3D printed part and outsourcing is money that can be invested in a high temperature 3D printer. Therefore, your “break even” cost can be determined by dividing the cost of the 3D printer by the per part savings. It should be noted that ULTEM™ 9085 is overengineered for many applications. So, when common engineering-grade materials like PA-CF cost more than ULTEM™, users of closed systems are forced into an unnecessarily long payback periods and diminished ROI.
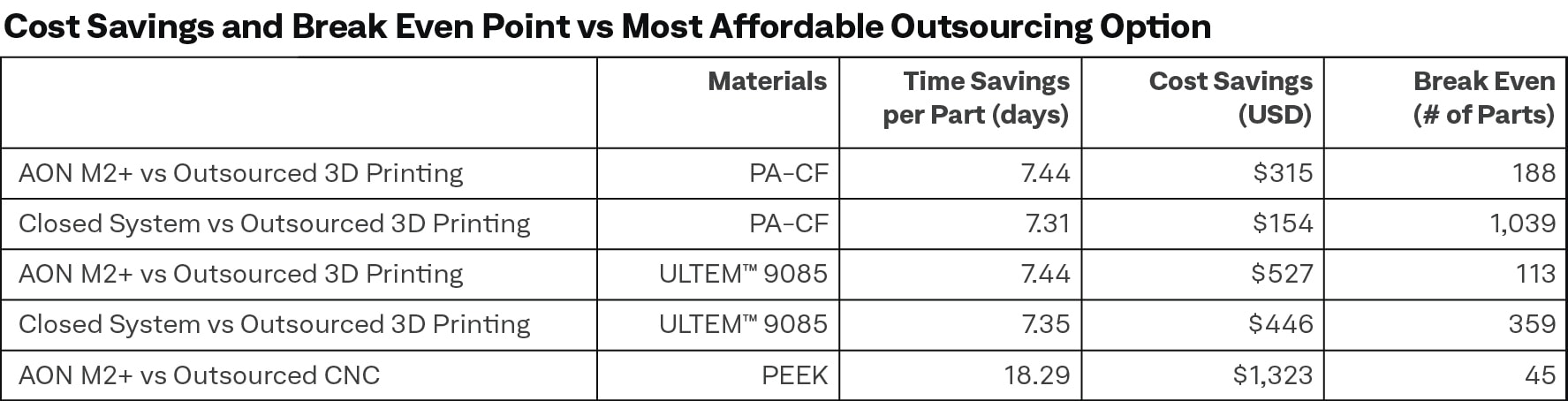
Conclusion
With the AON M2+ High Temperature Industrial 3D Printer, businesses can innovate faster and more affordably compared to conventional and outsourced manufacturing methods. The ability to print high performance materials enables engineers to print high strength, high temperature resistant parts suitable for even the most demanding applications, increasing the utility of additive manufacturing across an organization. Combine this with affordable hardware with high quality, low-cost material options, the AON M2+ payback period can be measured in months, not years.
Achieve New Levels of Part Performance & Throughput
3D print the world's highest performance polymers - bigger, faster, and stronger than ever.