3D Printing with PEEK, PEKK, & ULTEM™
Join AON3D's 3D printing application and materials experts for a 30-minute session that covers all the key information
Conventional manufacturing was cost and time prohibitive for pioneering the field of deployable space structures.
Additive manufacturing end-use carbon fiber PEEK composite tooling, manufacturing jigs, and test fixtures utilizing the AON M2+.
$4000+ and 4-6 weeks per composite mold.
The Customer:
The next space race is heating up with a bevy of new space-based businesses and missions to other planetary bodies. At the heart of this race lies a major engineering challenge — escaping earth’s gravity with space structures large enough to support next gen space travel and extraterrestrial colonization.
Opterus Research and Development, Inc., an aerospace business located in Loveland, Co., is taking on the challenge with a unique approach. Instead of larger spacecraft, Opterus designs and fabricates massive composite space structures that fit in extremely small payloads, which later expand in space.
As an example, Opterus can fit 40m (131.2 ft) rigid structural supports, known as Trussed Collapsible Tubular Masts (TCTM), into shoebox-size packages. With a mass of just 6.5 kg, Opterus provides a feasible and cost-effective means for sending large solar arrays, reflectors, antennas, and other structures to space.
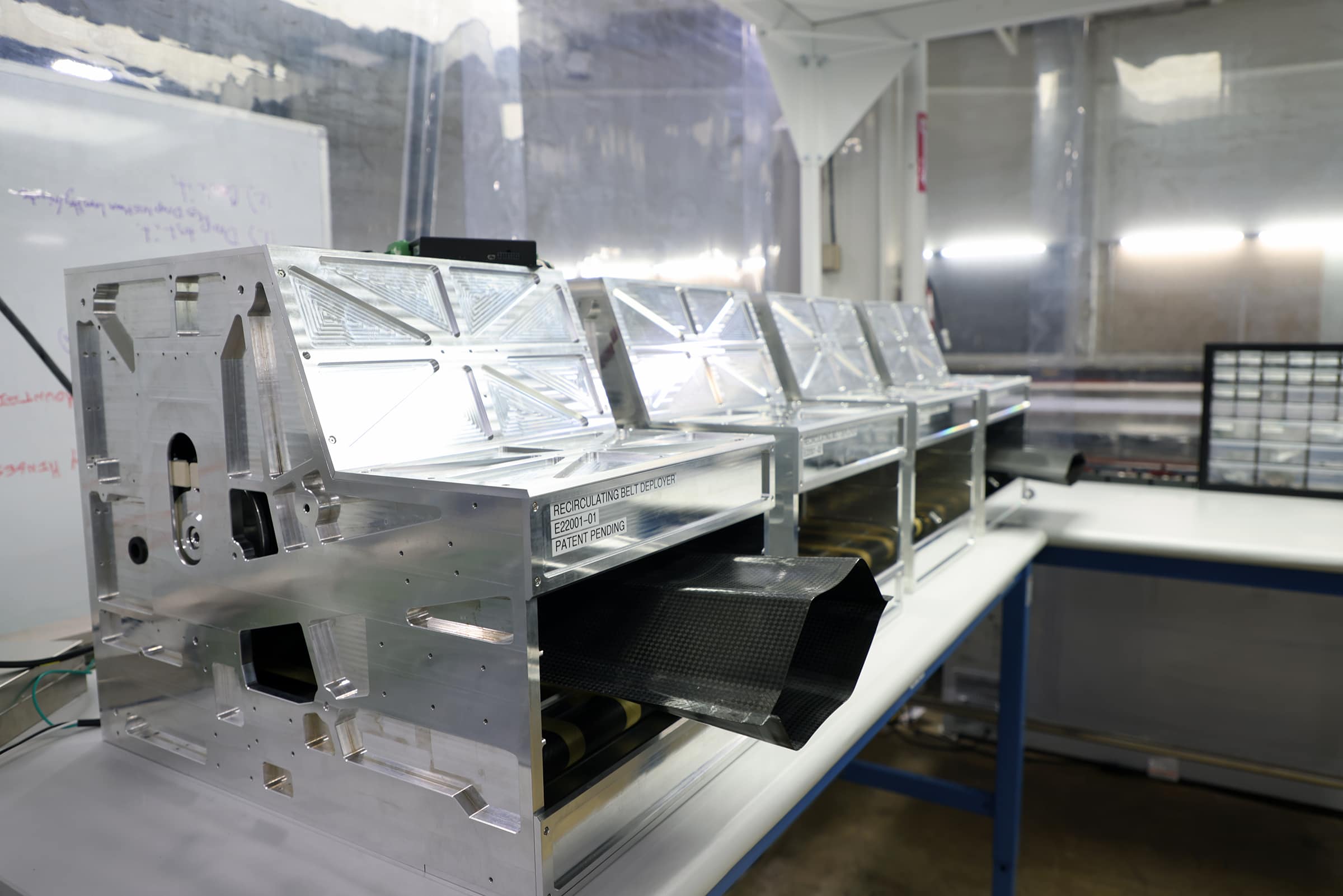
The Challenge:
In pioneering a new type of design, Opterus is solving problems for which no previous solutions exist. Each new project requires extensive research and development, testing, and custom tooling to complete.
Opterus’ deployable space structures are manufactured using advanced ‘High Strain Composite’ (HSC) materials offering 2x higher bending strains, 5x mass reduction, 8x stiffness, and 20x dimensional stability compared to conventional spring steels used in prior art deployable space structures.
To manufacture HSCs, conventional composite tooling offered limited design complexity while costing thousands of dollars and weeks to months per iteration. Inversely, desktop 3D printers were affordable and fast but only suitable for light-duty, low heat applications.
The Solution:
Opterus’ engineering team turned to high temperature 3D printing to develop their designs and manufacture low-cost, full-scale composite tooling. In their search, the engineering team found the AON M2+ with a sizeable 450 x 450 x 565 mm heated build volume and open access to engineering-grade and high-performance polymers.
Utilizing the AON M2+ and carbon fiber peek, Opterus manufactures composite molds for thousands of dollars less and weeks faster. CF PEEK’s properties were ideal for the application, with a low coefficient of thermal expansion (CTE) and ability to withstand curing temperatures that can exceed 180°C. After a bit of light sanding and J-B Weld or Teflon tape, the molds take minimal preparation from printer to prepreg layup.
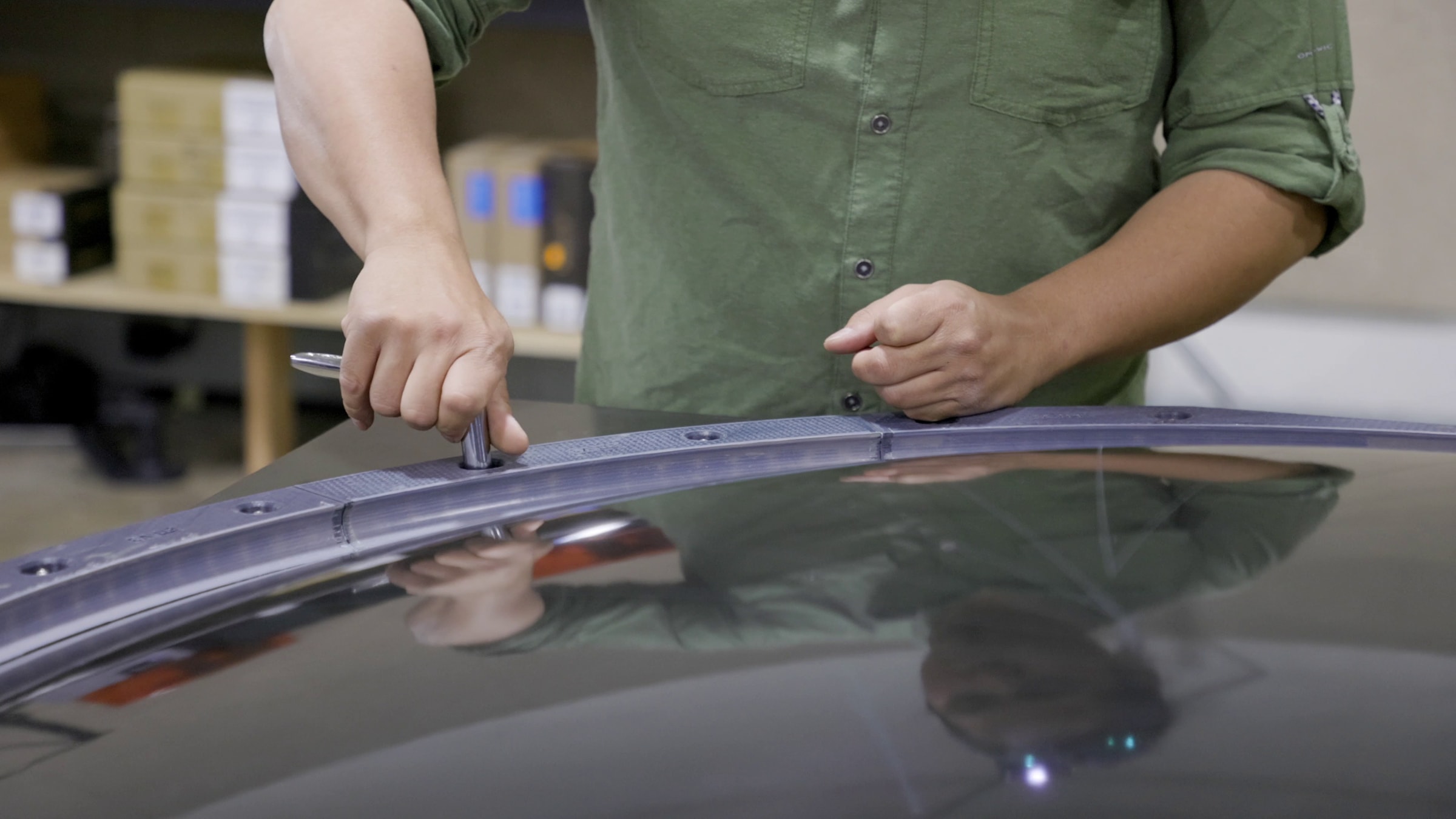
What’s Next:
With their technology and process, Opterus aims to bring the next generation of high performance space structures to market ranging from small satellite antennas to solar arrays up to 10,000 sqm (6.2 sq. mi.) for use in solar power beaming, solar sails, and in-space manufactured megawatt solar arrays.
The company is positioned to achieve initial space flight heritage by mid-2024 for novel, advanced deployable spacecraft structures including composite rollable booms, deployable parabolic reflectors, and deployable solar array structures for small and large spacecraft. These milestones will build upon years of new technology demonstration and maturation, adding to Opterus’ portfolio of products in orbit today.
Achieve New Levels of Part Performance & Throughput
3D print the world's highest performance polymers - bigger, faster, and stronger than ever.