3D Printing with PEEK, PEKK, & ULTEM™
Join AON3D's 3D printing application and materials experts for a 30-minute session that covers all the key information
Independent dual extrusion (IDEX) is a 3D printer configuration for material extrusion 3D printers (MEX) where two extruders can move independently of the other on the X axis. In terms of functionality, the IDEX system found on the AON M2+ provides the ability to print multiple materials or soluble supports with better print quality, speed, and reliability over fixed dual extrusion systems. In this article we look the benefits of IDEX and its advantages over fixed dual extrusion 3D printers.
Benefits of Dual Extrusion
Soluble Supports
Dual extrusion provides two very important features in 3D printing. First, it enables the 3D printing of breakaway or soluble supports. In MEX, each layer must be supported by the layer beneath it. When designs feature extreme overhangs or ‘bridges’ a support structure must be printed to hold up new layers while they cool and solidify. Support material comes in three basic forms:
- Soluble Supports – After printing, these ‘material scaffolds’ are dissolved, commonly in water, leaving a high-quality part surface with no manual labor needed. An added benefit of soluble supports is they can be placed in hard-to-reach areas, such as internal geometries.
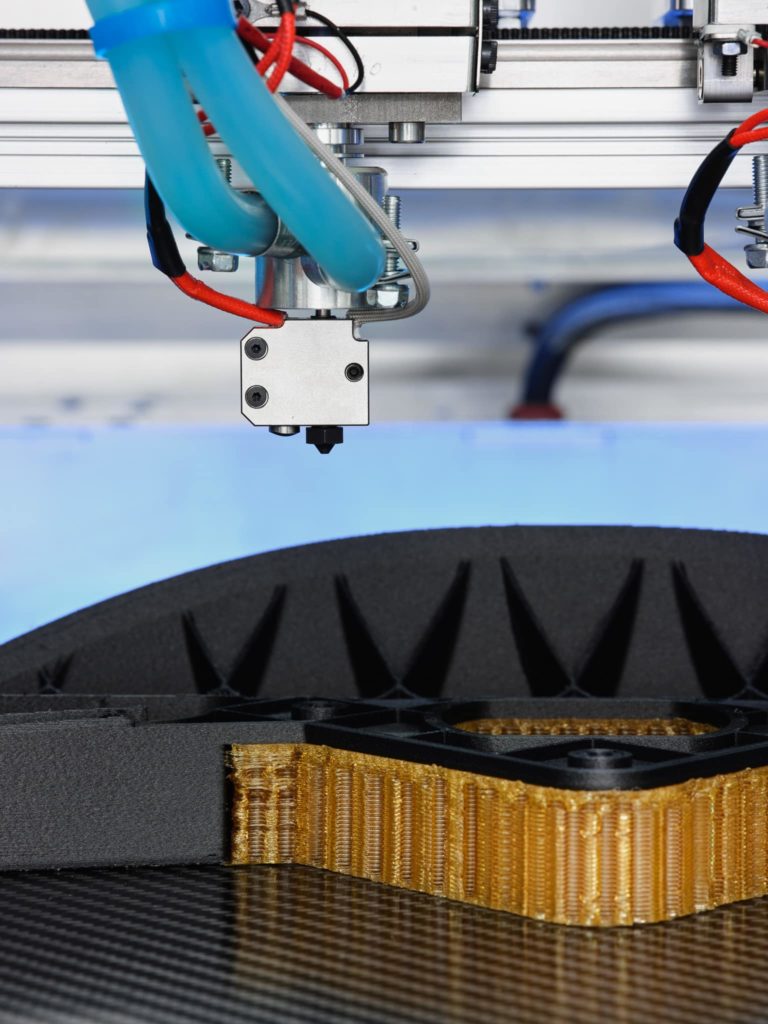
- Breakaway support – A support material designed specifically for easier removal, although removal can still be time consuming.
- Same material support – Single extruder 3D printers are limited to same material supports. In addition, some materials can only adhere to themselves, like Polypropylene. For these support structures, manual removal of supports is needed, can be time consuming / difficult to remove, results in poor surface finish, and can damage the model while removing.
Multi-Material Prints
Second, dual extrusion enables engineers to combine multiple materials in one print for localized and desirable material properties. For example, soft, flexible TPU components can be integrated into a high-strength fixture for holding irregular shaped parts. Or maybe you want to add a low-friction, self-lubricating Nylon to the exterior of a high-strength carbon fiber nylon gear.
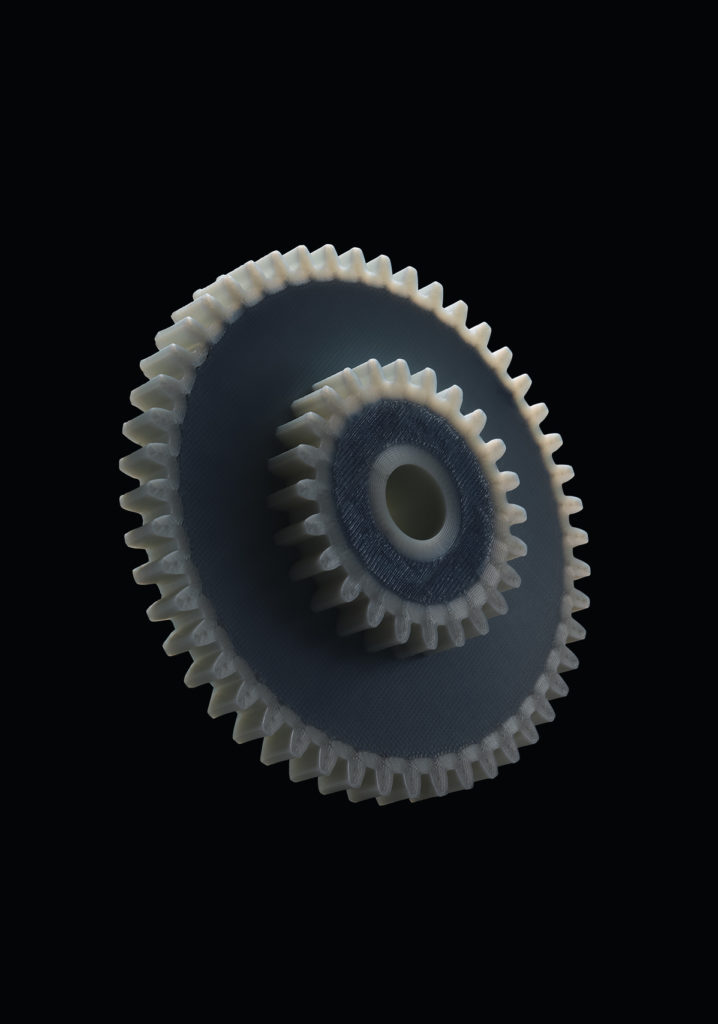
IDEX vs Fixed Dual Extruders – Reliability & Print Quality Comparison
An evolution of the fixed dual extrusion system, IDEX provides a number of advantages
Independent Dual Extrusion | Fixed Dual Extrusion | |
---|---|---|
Individual, low-mass extruders accelerate / stop / move quickly with minimal printing artifacts. | Print quality | Combined extruders, often with nozzle lifting mechanisms, contain more mass resulting in ghosting, ringing, rounded corners, and other print artifacts. |
Idle extruders wait off the build volume until ready to be used. At this point, nozzles are cleaned of any oozing material before resuming printing, providing clean layers and crisp material transitions. | Material Contamination | While idling, inactive nozzles often ooze material which then makes its way into the layers of the other material. |
Extruders wait off the build volume and far away from the other hot end. | Heat Bleed | Hot ends in close proximity, sometimes reaching as high as 500°C, heat the conjoined idle extruder, softening the material within its feed path, resulting in stripping of filament and failed prints. |
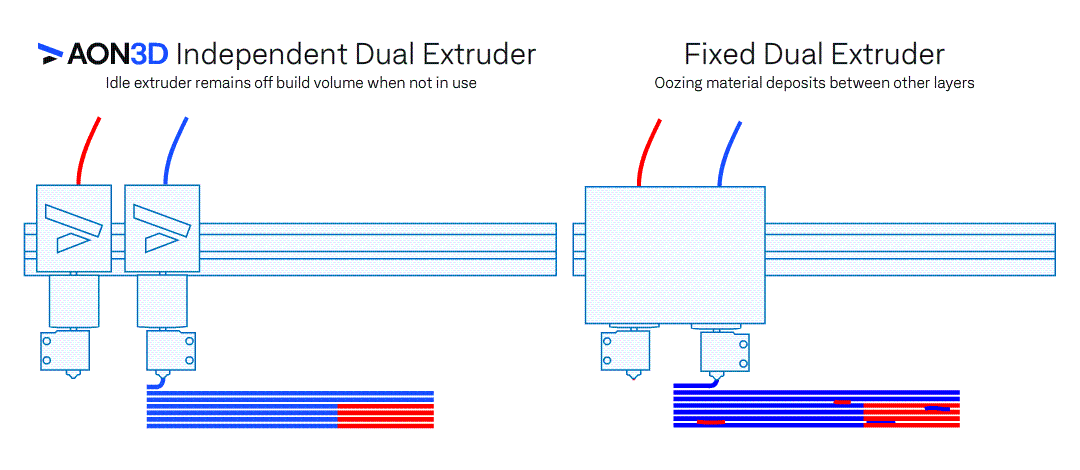
Summary
When assessing 3D printers, choosing a platform with the most application and material flexibility provides a fast-tracked return on investment. The AON M2+ with IDEX does just that, unlocking the ability to print complex shapes, large internal geometries, and multiple material parts with impressive print quality.
Achieve New Levels of Part Performance & Throughput
3D print the world's highest performance polymers - bigger, faster, and stronger than ever.