3D Printing with PEEK, PEKK, & ULTEM™
Join AON3D's 3D printing application and materials experts for a 30-minute session that covers all the key information
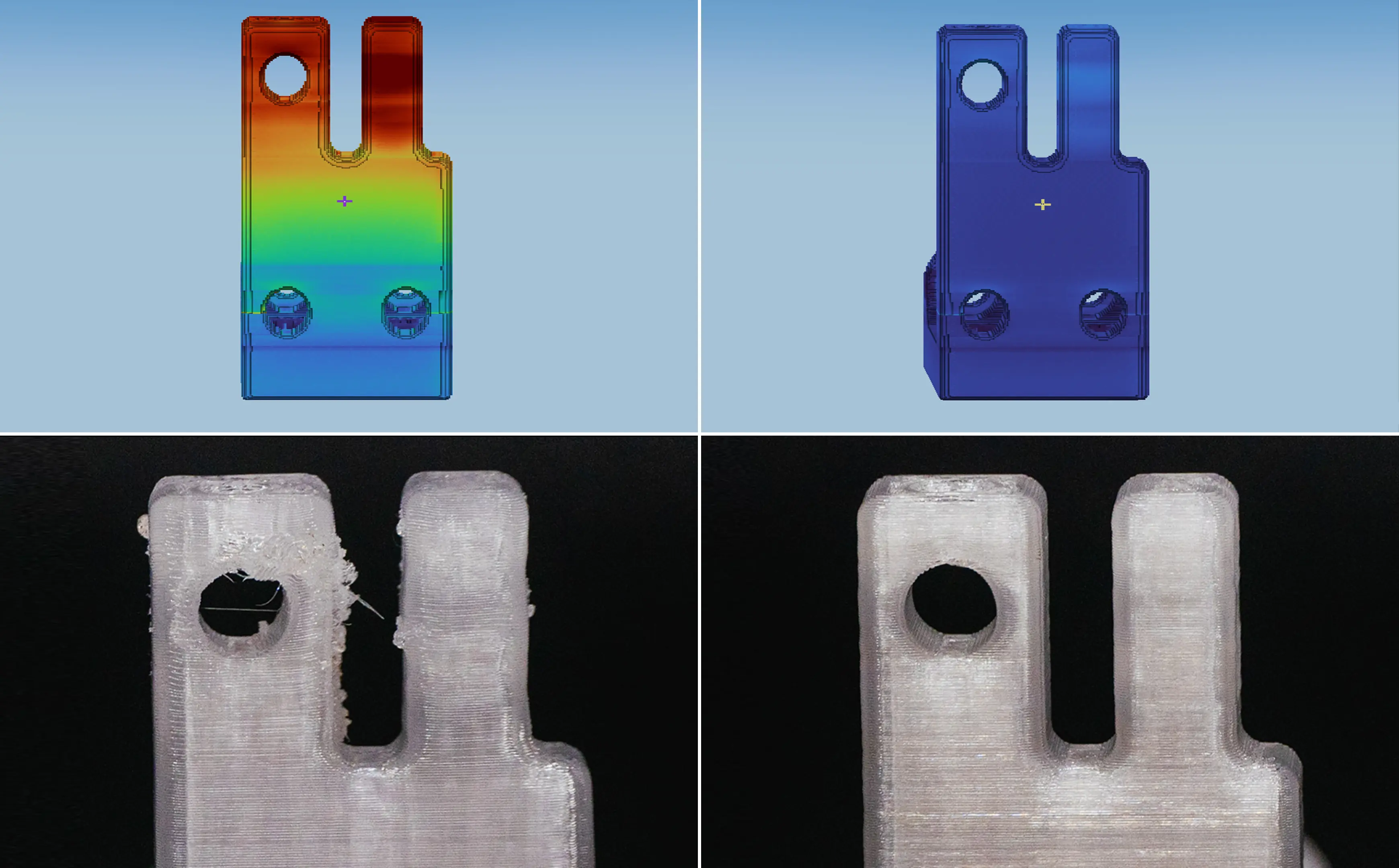
AON3D, a Montreal-based manufacturer of high temperature 3D printers, announced they will preview a new machine learning-driven thermal optimization software at RAPID + TCT 2023, a tool they say will lead to higher performing and more consistent parts in Material Extrusion (MEX).
The core technology is a simulation engine, built from the ground up specifically for MEX, that provides fast and accurate predictions on heat flow behavior throughout an object during printing. Unlike other software on the market today, AON3D’s hybrid modeling approach marries the proven accuracy and reliability of numerical methods with the speed and ease of use of statistical modeling.
The output can be used during the build preparation process for parameter optimization, pre-build QA/QC, post-build inspection, and more – offering several avenues to cut costs and scrap rates, improve reliability, optimize performance, and drive better technical decision-making.
The Missing Layer in Current Slicing
Build preparation software, often called “slicers”, offer varying degrees of analysis and optimization capabilities for operations such as the toolpath behavior, support placement, and other geometric aspects. What they are missing is an entirely separate dimension of thermal and heat flow behavior that should be optimized for, impacting final part performance, dimensional accuracy, and more. Instead, current slicing methodologies essentially use a “one size fits all” approach to apply thermal and speed parameters, or require painstaking manual interventions across specific sections of layers.
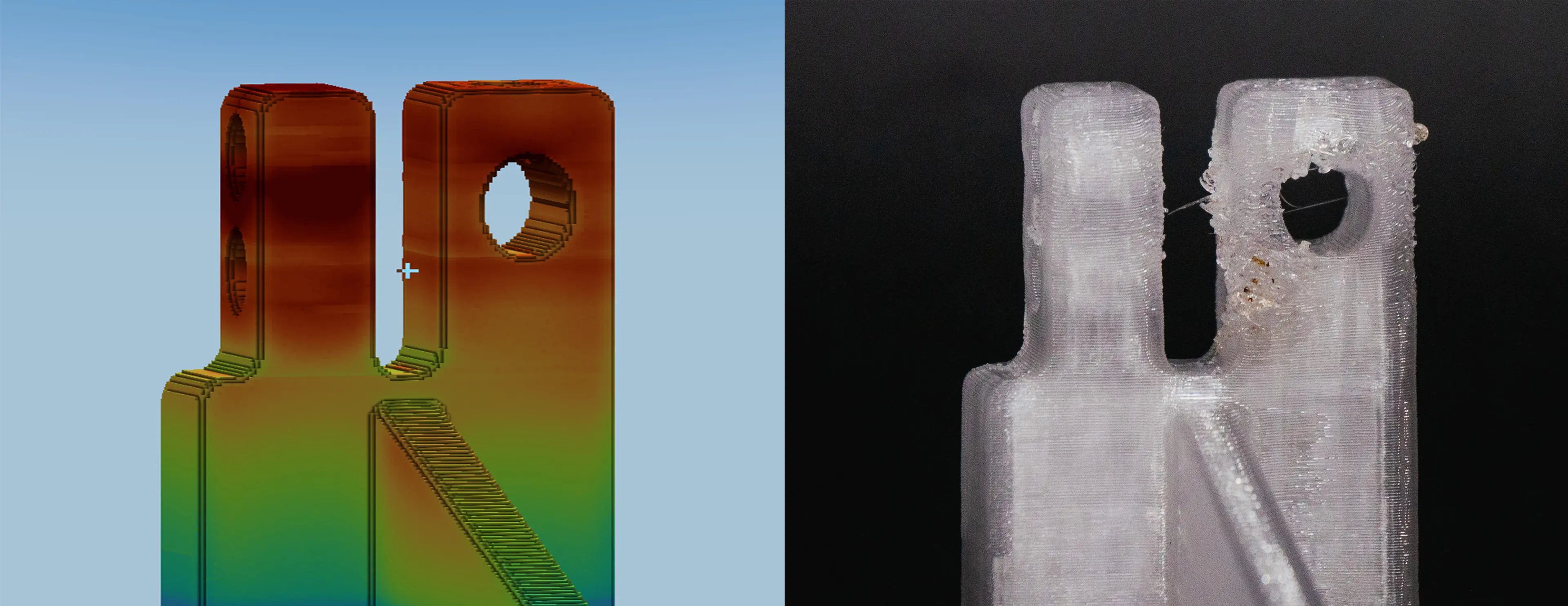
Achieving Consistent, Higher-Performing Parts with Thermal Intelligence
Starting from just a G-code file, AON3D’s software will provide users with a full visualization of the temperatures and heat flows throughout a part. This makes it easy to see how process decisions connect to specific outcomes, and either take corrective action before the print or define inspection requirements for after the print.
AON3D’s software can also output fully structured data in raw form for use in other analytical software such as structural FEA, or custom post-processors.
Generated data will be available at spatial resolutions down to 1/3rd the width of an extruded polymer bead. Unlike a layer-by-layer approach, this transient simulation inherently accounts for complex part features and regions leading to strong and dimensionally accurate parts.
AON3D is also tackling composite & semi-crystalline polymers – two categories that have historically proven challenging for modeling and simulation, including some of the most popular choices such as PEEK, Nylon, PAEK, and PEKK.
Reducing the Downstream Quality Management Burden
AON3D’s new software will enable engineers to make informed design and process optimization decisions by incorporating an entirely new form of quantitative data. When used with the AON M2+ High Temperature 3D Printer and Readyprint™ filaments, manufacturers can achieve a new level of consistency and part confidence across machines and production runs, reducing the need for time-consuming testing and quality management.
Preview the new software at RAPID + TCT in Chicago, May 2nd – 4th, in booth #4241.
Achieve New Levels of Part Performance & Throughput
3D print the world's highest performance polymers - bigger, faster, and stronger than ever.