3D Printing with PEEK, PEKK, & ULTEM™
Join AON3D's 3D printing application and materials experts for a 30-minute session that covers all the key information
Polyetheretherketone (PEEK) is regarded as one of the highest performance thermoplastics due to its incredible mechanical, chemical, thermal, and weight-saving properties. That said, final part properties of PEEK are not guaranteed by simply 3D printing the material. A printer’s ability to achieve specific chamber, bed, and nozzle temperatures will determine a part’s level of crystallinity and desirable properties. In this article we analyze 3D printer requirements and optimal temperatures to print high quality, mechanically robust PEEK parts.
To better understand how we can maximize the properties of 3D printed PEEK we must first understand crystallinity. Already familiar semi-crystalline and amorphous PEEK phases? Jump to ideal printing conditions.
Semi-crystalline vs Amorphous PEEK
The degree of crystallinity in PEEK directly influences its mechanical and chemical properties. Crystals are folded polymer chains that organize into packed, ordered structures as shown in the image below. Ordered polymer chains are linked together by chains that are randomly orientated, labelled as the amorphous phase of the polymer. PEEK can have both crystalline and amorphous phases in its structure, known as a semi-crystalline solid. PEEK can also be amorphous, where it has little to no crystallinity in its structure.
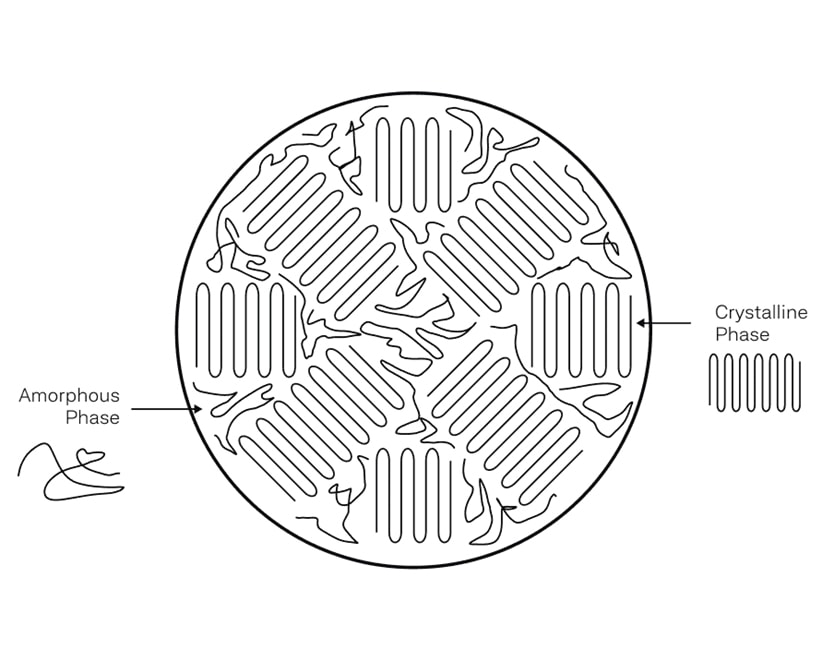
Semi-crystalline PEEK: Maximizing Part Properties
In semi-crystalline form, PEEK exhibits its best mechanical, chemical and thermal properties.
From the theory of polymer physics [1], polymer chains in the crystalline phase are aligned and form stronger intermolecular bonds, resulting in greater strength and rigidity. On the other hand, the polymer chains in the amorphous phase can be stretched and broken with minimal loading because of weak bonding and entanglement.
This structural difference allows semi-crystalline PEEK to withstand higher tensile stress, creep, temperature, radiation, and chemical resistance compared to amorphous PEEK. For example, semi-crystalline PEEK can be used under conditions up to 240°C but amorphous PEEK will begin to crystallize and deform at temperatures above 150°C.

In-situ Crystallization: Ideal 3D Printing Conditions for PEEK
Crystallization in polymers occur between the glass transition and melting temperature, where the polymer chains begin to fold and arrange. In-situ crystallization is the organization of these polymer chains, creating a crystalline phase during the 3D printing process. In PEEK, the crystallization process is rapid which results in a large specific volume change during solidification at Tm. Our materials scientists recommend a minimum chamber temperature within 10°C of PEEK’s glass transition temperature.
To achieve in-situ crystallization of PEEK and maximize part properties a build chamber temperature and bed temperature of 133°C or higher is needed. The extrusion temperature for PEEK 3D printing should fall in the range of 365-440°C.
3D Printing PEEK at Colder Temperatures
3D printers that are not able to achieve a build chamber temperature of 133°C or greater produce amorphous PEEK. As a result, almost every PEEK property is affected by decreased crystallinity, reducing tensile strength, flexural, heat resistance, chemical resistance, density, and even coefficient of friction.
In addition, printing PEEK at lower temperatures induces larger temperature gradients between the newly deposited layers and previously deposited layers. If polymer solidification and cooling is too rapid, three issues will arise:
- Part distortion due to the temperature differences between layers. Printed layers will cool down and contract relative to warmer layers printed above.
- Residual stress in the component due to the large temperature gradient.
- Z-direction strength decreases substantially as a larger temperature difference between layers reduces the interlayer polymer weld strength.
Therefore, the ambient temperature in the printer must be high enough to facilitate the crystallization of PEEK as well as to ensure optimum interlayer weld strength for high part isotropy. If a printer can only produce amorphous PEEK, the part properties will not allow for end use applications.
Annealing Cold Printed PEEK and Part Deformation
Under cold printing conditions, polymer chains are frozen in their disordered arrangement and lack the thermal energy necessary to organize a crystal structure. To crystallize an amorphous solid, the material requires post processing heat treatment at temperatures between Tg and Tm. This process is cold crystallization and is similar to the annealing heat treatment for metals.
The caveat of cold crystallization is that while a higher degree of crystallization can be achieved from an amorphous print, part distortion will be significant. As the amorphous phase in the polymer transitions towards an ordered crystal phase, there is a shrinkage in the volume of the part shown by the change from V1 to V2 in the graph below. This shrinkage translates to distortion in the final component after the cold crystallization stage which mitigates the near-net shaping advantage of 3D printing. Therefore, maximizing in-situ crystallization reduces the need for cold crystallization and is recommended for PEEK 3D printing.
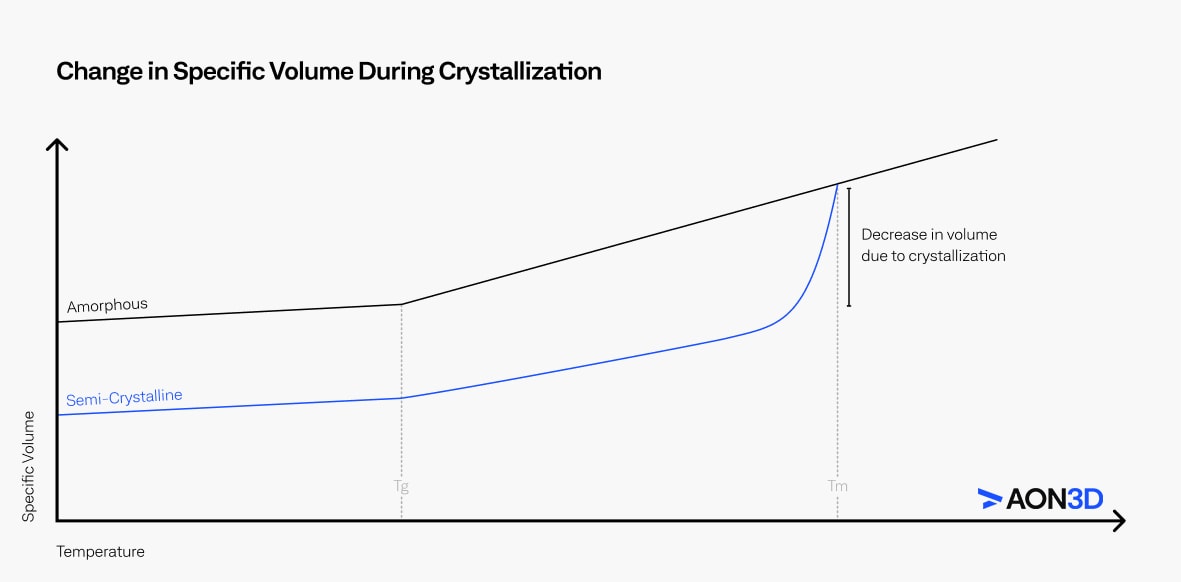
Conclusion
3D Printing PEEK at colder temperatures (below 133°C) reduces almost every desirable material property, including strength, isotropy, chemical resistance, and more. Cold printed parts can be annealed to increase crystallinity and restore some of these desirable traits but may result in significant part deformation. For this reason, in-situ crystallization of PEEK is recommended and can be achieved by maintaining a static build chamber temperature of 133°C or higher throughout the printing process.
References
Achieve New Levels of Part Performance & Throughput
3D print the world's highest performance polymers - bigger, faster, and stronger than ever.